DCX3 aseptic bearing shut-off valve are used in a wide variety of process and ancillary fluid applications, designed for efficient cleaning. The aseptic bearing shut-off valve is fitted with a fluid (cleaning/rinsing) or vapor circulation bearing. This configuration allows for sterilizing the valve components in contact with the exterior before encountering the fluid process when handling the valve.
DCX3 aseptic bearing shut-off valve – Definox
Features
- Same features as standard DCX3 (floating seal, thick body, etc.)
- Fitted with an aseptic guide bearing which steam or fluid (washing – rinsing) circulates through to clean the parts of the plug, which come into contact with the outside environment on the valve outstroke. When the valve closes, the steam in contact with the outside environment is sterilized before penetrating the valve body.
Option
-
- Cooling bearing
The DCX3 aseptic bearing changeover valve is fitted with a fluid (cleaning/rinsing) or vapour circulation bearing.
– Dimensions: SMS – DIN – US; from DN25 (1″) to DN150 (6″)
– When closing the valve, the plug stem in contact with the medium is sterilised before penetrating inside the valve.
– Possibility of fitting the valve with a cooling bearing.
– The fluid or vapour circulation bearings ensure cleaning of the parts of the plug in contact with the external environment when the valve operates.
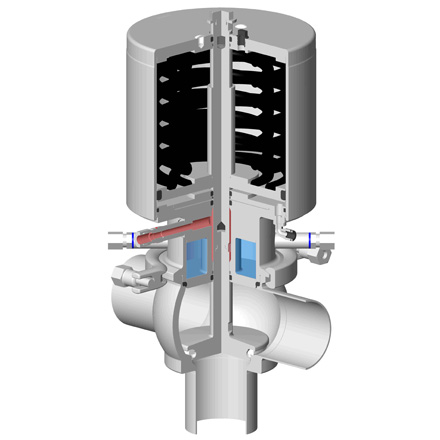
Technical Advantages DCX3 aseptic bearing shut-off valve
Materials
- Half body: stainless steel 1.4404/316L
- Disc: stainless steel 1.4404/316L
- Seal: EPDM – fluorinated elastomer (FKM) or silicon
- Operating devices: stainless steel 1.4301/304
Service conditions
- Max. temperature: +140oC/+284oF (temperature depending on seal type)
- Min. temperature: -5oC/+23oF
- Max. working pressure: 8 bar (800 kPa)/116 psi
- Actuator air supply pressure: min. 5.5 bar (550 kPa) /80 psi; max. 8 bar (800 kPa)/116 psi
- Vacuum resistance: 0.4 cm3/s

Replacing pfa seals DCX3 aseptic bearing shut-off valve
To change PFA seals, follow the guidelines given below:
• Remove the defective seal using a cutter taking care not to mark the bearing surface of the plug (protect the stainless steel surface using the edge of a steel rule or a plastic off-cut),
• Place the new seals in an oven at 140°C (+/- 3%) for 30 minutes. Do not exceed 200 °C. If the temperature is too low, there is a risk that the seal will deform or tear during installation.
Application of DPAX DE double sealing butterfly valve
With the above outstanding advantages, defines valves are very popular with investors in many fields such as:
– Food, pharmaceutical, chemical, and cosmetic industries
– Animal feed processing industry,…
*Technical team/consultant Thai Khuong Pumps is ready to connect to support you with information about industrial pumps in the fastest way. Contact Thai Khuong Pumps immediately, so we can better assist you.